The automobile torsion bar spring is a part that uses the torsional elastic deformation of the rod to act as a spring. The quenching and pre-twisting are important processes for processing the torsion bar spring. Manufacturers usually use conventional quenching and pre-twisting at room temperature. The disadvantages are: easy to cause torsion bar bending, uneven hardness, fatigue resistance, and large amount of slack. This paper solves this kind of problem by using rolling quenching and hot pre-twisting.
Current status of manufacturing process of torsion bar spring
Automobile torsion bar springs can be divided into two types: solid torsion bar and hollow torsion bar. The cross section has round, square, rectangular, elliptical and polygonal shapes, and the cross section is mostly round. Compared with the coil spring and the leaf spring, the torsion bar spring has a simple structure, no friction during operation, stable spring characteristics, no chattering, large energy storage per unit volume, small spring volume, and is a small and lightweight product in automobiles and trains. , tanks and armored vehicles have been widely used.
The manufacturing process of the torsion bar spring usually used by the manufacturer: cutting material (→ upsetting → annealing) → end processing → conventional quenching → tempering → normal temperature pre-twisting (strong twisting) treatment → shot peening → inspection → rust prevention.
There are disadvantages in the conventional quenching and normal temperature pre-twisting processes in the process route:
1) Conventional quenching usually has three methods: hanging vertical into quenching liquid, horizontal horizontal entering quenching liquid and high frequency induction hardening. Hanging type quenching, there will be uneven hardness on the upper and lower sides of the workpiece, which is "S"-shaped bending, which is difficult to straighten; horizontal horizontal quenching, because the workpiece is subject to different cooling ability, it is easy to deform; high-frequency induction quenching will appear torsion bar The phenomenon of quenching is impervious.
2) Pre-twist (also known as strong twist) is one of the most important methods for strengthening the torsion bar spring. The purpose is to improve the pre-compression stress of the surface layer of the torsion bar and to develop the bearing potential of the core material to improve its fatigue resistance and maximum allowable shear stress. The method is that after the heat treatment of the torsion bar, a torsion angle is applied along the bearing direction of the working at normal temperature (greater than the maximum working twist angle when used), so that the surface stress of the torsion bar exceeds the yield limit of the material and plastically deforms, and then Uninstall. After continuous loading and unloading, the plastic deformation of the surface layer of the torsion bar tends to be stable, and the slack deformation after the last unloading is guaranteed to be less than the specified value. The disadvantage is that the number of pre-twisting times is more than three times, which prolongs the manufacturing cycle of the product, wastes manpower, material resources and financial resources, and has large slack deformation and weak fatigue resistance.
New technology for torsion bar spring manufacturing
The new process of torsion bar spring manufacturing is to replace the conventional quenching with rolling quenching, and to replace the normal temperature pre-twisting with hot pre-twisting, and the other processes are unchanged.
1. Rolling straightening quenching
For the conventional quenching problem of the torsion bar spring in the process route, the torsion bar spring rolling straightening quenching is provided. The structure of the device is shown in the figure, consisting of five parts: speed regulation, straightening, bed, quenching and lever. The speed regulation part includes the motor, the transmission, the driving gear and the driven gear; the straightening part includes the driving shaft, the end cover, the driven shaft, the slider, the U-shaped sealing ring, the driving wheel and the flat key, the driven wheel and the flat key, the bearing , U-ring seat, slider, shaft circlip and counterweight; quenching part includes spray pipe; lever part includes wire rope, lever bracket, lever and foot pedal.
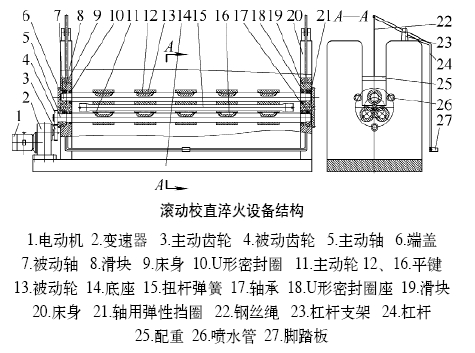
Rolling straightening quenching equipment structure
The transmission is mounted on the base, the motor is directly connected to the transmission, and the driving gear on the transmission is simultaneously coupled with the driven gears on the two driving shafts, so that the driving directions of the two driving shafts are the same, the speed of the transmission can be adjusted, and the principle of adjusting the speed is twisted. The rod spring can rotate freely and is not thrown, generally about 40r/min. The straightening part of the power is transmitted from the driven gear of the speed regulating part to the two driving shafts. Both the driving shaft and the driven shaft are equipped with bearings and U-shaped sealing rings at both ends. The main and driven wheels, the driving shaft and the driven shaft are made of Hot work die steel or stainless steel; the driven shaft and the driven wheel have a larger diameter than the drive shaft and the drive wheel in order to increase the straightening pressure; the length of the main and driven wheels is 80-100 mm, the gap is 80-100 mm, and the drive shaft and The driven shaft can be finely adjusted; the distance between the two straight rods of the torsion bar spring and the driving wheel and the driven wheel should be as close as possible, generally not more than 10 mm; the three spray pipes of the quenching part are evenly distributed around the axis of the torsion bar spring. On the cylinder, the two ends are fixed on the bed body, and the water spray speed and pressure of the spray pipe can be adjusted. The coolant in the spray pipe can be water or other quenching liquid.
2. Thermal pre-twisting
Compared with the normal temperature pre-twist, the hot pre-twist can reduce the number of pre-twisting, only one hot pre-twist and one normal temperature pre-twist, improve the fatigue resistance of the automobile torsion bar spring and reduce the amount of slack.
The technical solution for hot pre-twisting treatment is: tempering the automobile torsion bar spring at 450~480 °C, using industrial robots or workers wearing high temperature resistant gloves to put the torsion bar spring into the torsion testing machine for hot pre-twisting, torsion bar spring when twisting The surface temperature is controlled at 250-270 ° C; after the hot pre-twisting, a normal temperature pre-twist is performed, and the twist angle is smaller than the hot pre-twist angle, but greater than the maximum working twist angle when used.
The method is suitable for small batch production. If it is used in an automatic production line, it is only necessary to change the lever part to hydraulic transmission and increase the automatic loading and unloading device.
3. New process effects
Rolling and straightening quenching uses the rolling action of the driving wheel and the driven wheel to pre-roll the straightening torsion bar spring in a red hot state, which functions as pre-cooling and equalizing temperature. The water spray or quenching liquid is sprayed on the three spray pipes uniformly distributed on the cylinder centered on the torsion bar spring axis, the quenching thermal stress is small, the torsion bar spring has less bending, the deformation is small, and the full length straightness is smaller than 0.5mm, uniform hardness, low equipment investment, simple operation, and improve the fatigue resistance of the torsion bar and reduce the amount of slack.
Hot pre-twisting treatment by using industrial robots or workers wearing high-temperature gloves, the torsion bar spring is loaded into the torsion testing machine for a hot pre-twisting, and then a normal temperature pre-twisting, equipment investment is small, the operation is simple, and the product manufacturing cycle is shortened. Improve the fatigue resistance of automotive torsion bars and reduce the amount of slack.
For the company, one type of torsion bar spring is divided into two groups (five samples per group), and the original process and new process are respectively used for test verification. The first group is subjected to conventional quenching and three times of normal temperature pre-twisting; the second group is respectively subjected to rolling straightening quenching, and the same thermal pre-twisting and normal temperature pre-twisting as the first two angles of the first group are performed, respectively, and the test results are attached. table.
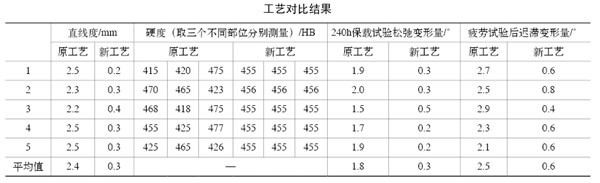
As can be seen from the results in the table, the average straightness of the first group is 2.4 mm, and the second group is only 0.3 mm; the hardness of the first group is uneven, and the hardness of the second group is uniform and the change is small. The load-bearing test was performed by twisting the same angle and maintaining 240 hours. The average relaxation deformation of the first group was 1.8°, and the second group was only 0.3°. The fatigue test was performed separately, and one end of the torsion bar was fixed, and the torsion bar was added by the cam lever. Force, the torsion bar is rotated 45°, free to rebound, and after 50,000 reciprocations, the hysteresis deformation is measured. The first group average is 2.5°, and the second group average is only 0.6°.
Through the above research, the performance parameters of the new torsion bar spring manufacturing process in straightness, hardness, relaxation deformation after 240h load test, fatigue resistance and other aspects are significantly better than the original process, indicating that rolling quenching and hot pre-twisting can effectively solve Problems in the processing of torsion bar springs.
Furniture Handles
Furniture handles have a strong aesthetic effect on the appearance of furniture. This is because the choice of furniture handle has an important relationship with the shape, color and position of the furniture. Therefore, it is very important to choose furniture handles. The door handles with good quality and good style are not only convenient to use, but also add the finishing touch to the overall beauty of the cabinet. We have strict quality control from material processing, polishing, assembly and packaging. Extensive experiences, mature technology and professional service allows us to meet the different needs of customers of different regions. Special requirements and sizes are available. Please just feel free to contact us if you have any question. Our team is on call for 24/7 to provide the worry-free before/after-sale service.
Handles For Furniture,Kitchen Cupboard Door Handles,Kitchen Cabinet Pulls,Black Cabinet Pulls
Leader Hardware Manufacturer Limited , https://www.leaderhardwarecn.com