In the perception of the average consumer, the American auto parts manufacturer, Sida, is not as well known as Bosch in Germany. But in the eyes of professionals, its expertise is unique. As the only supplier of diesel engine oil pump and emission control systems in Cummins worldwide, Stanley is focused on providing high-precision engine fuel injection systems and emission control systems to customers worldwide, including GM, Ford, Volkswagen and other world-class vehicle manufacturers. In 2007, after investing in Sida Precision Electromechanical (Changshu) Co., Ltd. (hereinafter referred to as Changshu Sida), it officially entered a period of rapid development in the Chinese market.
At present, Changshu Sida is mainly engaged in the production of high-precision fuel system components (control pump parts), such as pump casings for medium and heavy trucks, camshafts, fuel pumps and fuel injectors, which are supplied to the Chinese and North American markets. The average annual production of DCR fuel pumps is 70,000, with a development target of 100,000. In addition, the average annual production of PN injectors is 360,000.
Adhering to the high requirements of the headquarters for superior quality and production efficiency, Changshu Schneider continues to optimize the supply chain in terms of precision machining and assembly. Ji Zengliang is the person in charge of the company's supply chain optimization project. He said: "Precision is the unshakable technical requirement of the company's products. Our products need to achieve μ-level precision in machining, and the precision of assembly is extremely high, which makes the products extremely Stability. At the same time, improving the price/performance ratio of products is a must to win more orders and gain a dominant position in the market competition. Our product positioning is medium and high-end, and thus, especially in the Chinese market, it is more important to reduce the cost per piece. This is the focus of our work."
Crack high cost
The DCR product design was introduced from abroad, but the product line and processing assembly were all completed by the Changshu factory itself. After three years, the company began mass production at the end of 2013, mainly for Cummins. However, the material of the forged steel DCR product has high hardness, complicated processing shape, and many deep holes and intersecting holes, and the processing cost has been high. “Optimizing on mature projects and reducing costs to set goals, the challenge seems to be bigger.â€
For example, the cross deep hole processing of the DCR fuel injection pump cover is a typical processing difficulty encountered by Changshu Sida. Yang Yong, who specializes in DCR product technology and technology, said: "No matter which industry is processing cross-deep holes, especially large-angle cross-deep holes are a relatively large processing difficulty. It took us more than a year to solve this problem. ."
This difficulty lies in the DCR pump cover (shown in Figure 1), the material hardness is 40HRC, there are oblique cross holes, the angle is 120 degrees, the processing hole depth is 84mm, D4, 21 times diameter. Since the second hole is processed, because of the cross hole and the heat treatment hardness is relatively high, it is generally easy to break the knife, especially to check the centering of the Drill Bit and the support ability of the through hole edge belt.
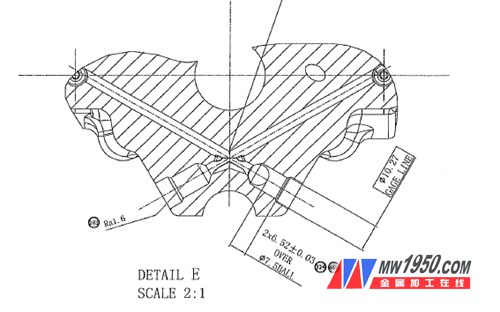
“Before the cost loss caused by this product is very large, the main problem is the drill bit. Even if the initial budget is sufficient, the average cost of the Tool will exceed 80,000 to 90,000 per month. Now it is new. After the tool brand, not only the cost per piece has come down, but also the processing cycle has been well adjusted. The cost of the whole project has dropped from 130 yuan at that time to the current 70 yuan, which is successfully controlled within a reasonable budget. Life expectancy has also improved a lot.†Tan Satisfaction is the person in charge of Sida's tool optimization.
And the new tool he said is Walter's new DC170.
Knocking on the door
It is precisely because of the excellent performance of DC170, not only let users praise him, but also knocked out the full application of Walter tool in Changshu Sida - all existing tools are replaced by Walter series products.
The DC170 was introduced in October 2014 and is the first representative of the new level of efficiency for the Walter Group's carbide machining tools. The belt has a unique design with a unique annular blade structure and is unique in the current market. Compared to conventional geometrically shaped carbide drills, the DC170 is more reliable, stable, smoother and more efficient. The new drill bit is internally cooled. The gentle groove makes the cooling lubricant flow evenly while avoiding dangerous scum obstacles. The novel design of the blade allows the coolant to be continuously flushed from all directions, even at extreme temperatures, and the cooling effect is very good. In addition, the change in the land structure also causes the vibration caused by the machining to be continuously guided and reduced to a minimum level, so that the rotation of the drill bit is more stable and the stability of the tool operation is also ensured.
Xia Juntao, Walter is a senior technical expert in the Suzhou area. He is the main implementer of the Sida's optimization project. He said: "The requirements for tool cover processing are relatively high, because orthogonal vertical is not difficult, it is rare. The through hole is slanted. The general tool includes the radial force generated by the drill bit when it is often unable to withstand the beveling process, and the blade is broken.
It is understood that the construction and processing of this pump cover product originated from Bosch in order to fully burn the entire fuel system. But even in Bosch's manufacturing plants, the phenomenon of machining broken knives is difficult to avoid, and coordination stability is a difficult problem in the world.
“The DC170 was designed specifically for this purpose. After three years of research and development, it was successful. It is suitable for the processing of steel and cast iron materials in all industries, such as through holes and exits, which are difficult to process.†Xia Juntao Continue to introduce, "After more than a month of testing, the DOC170 has been applied in batches on Changshu Sida pump cover products."
Now DC170 can achieve 350 holes, which is more than double the life of 160 holes of the original tool, while improving efficiency and accuracy. In addition, the DC170 drill has eight distinct annular grooves to provide optimum operating temperature and is also useful as a retreading scale. The DC170 drill can be refurbished three to five times until there are only two annular grooves left. In this sense, users can fully tap the potential for refurbishment, thereby further reducing production costs.
Seamless
Since this is the product of Walter's entire line of Changshu Sida, what about the performance of other products other than DC170? For this problem, Tan satisfied with affirmation: "It is also very good. For example, an NC drill bit, the original life is 200 workpieces, and now Walter's semi-non-standard coating design life can be increased to 1,300 workpieces, the life is The original 6 times or more. Now after all the tool changes, the cost of Changshu Sida tool has been steadily decreasing, and the monthly savings amount is on average more than 120,000 yuan."
At present, the processing cost of a single piece of Changshu Sida DCR fuel pump is about 40 yuan. If it is based on the annual output of 100,000, it will be a number that cannot be underestimated. Tan Satisfied said that as a precision machining company, tool costs account for a large proportion, and other costs may be auxiliary costs, which is the main reason why companies pay so much attention to tool costs.
Precision machining often requires the final process to be completed by grinding. Now, some parts made by Changshu Sida are basically within the range of 0.006mm. Since the influence of pre-processing on the stability of subsequent processes is more critical, the two parties are exploring new processing methods to ensure the position of the processing and reduce the processing difficulty of the subsequent processes.
Challenge impossible
According to industry practice, when the tool is usually improved, the improvement range is between 10% and 15%. It is very rare to achieve 100% improvement. “Because of the replacement of the overall brand, it is now necessary to ensure the smooth transition of the tool change, and then look at the life of the tool.†Yang Yong said, “The beat optimization has been completed before, the requirement for Walter must reach the existing Production beats."
After completing all the tool switching, Changshu Sida was spent more than three months, and the cost was improved. The original project used 63 tools, and now it is switched to 48, and the improved part is about 7 or 8 kinds. . “A project switches all the tools, usually at least six months to a year, we only used three months.†Tan said. This is a testimony to Changshu Sida's excellent management level and production level, and also a powerful explanation for its partner Walter's strength.
Xia Juntao said frankly: "When Changshu Sidani proposed to change the model, we did have a lot of pressure. The whole industry, including Walter, did not have a complete three-month handover. At the beginning, our reaction was impossible."
However, "not enough research, can not say no to customers" is the principle that Walter has always pursued. Walter first sent technicians to understand the product structure and all the processing, including discussing the relationship between size and size and the process of arranging between the knife and the knife. After getting the first-hand information, the staff also mobilized the experts of the German headquarters to solve the difficulties and developed a comprehensive solution. “After the operation of this project, almost every tool has been tested, which is unprecedented, because usually a lot of tools are not tested in a project.†Tan Satisfied, “Because it is an optimization improvement project, our goal Yes: the cost must be low, and the efficiency must be high. From an experimental tool to every technical engineer, from the timeliness of delivery to the delivery of non-standard tools, Walter can say that they have fully played their 'Advantageous technical ability'."
"More importantly, we think this is actually a kind of stimulation of both sides' ability. If neither party can do it, there is no way to do it. For example, Yang Yong is very familiar with this product, every detail is familiar with the chest, and provides us with A lot of help.†Xia Juntao said that after Walter personnel settled in, Changshu Sida's procurement and technical departments fully cooperated with the progress of the project. Once there were technical problems, the three parties discussed and resolved on the spot, without repeated waiting, the miracle of three months came naturally.
After handing over all the optimization tasks of the tool to Walter, Starron is looking forward to a higher level of core competitiveness.
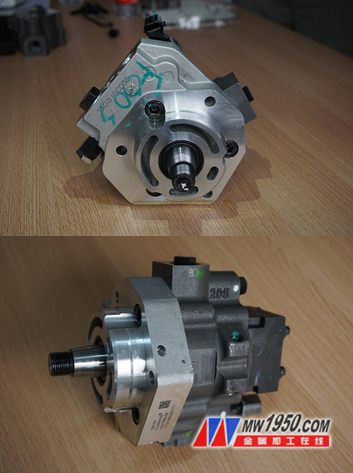
Figure 1. Stanley is focused on providing high-precision engine fuel injection systems with high demands for superior quality and productivity.
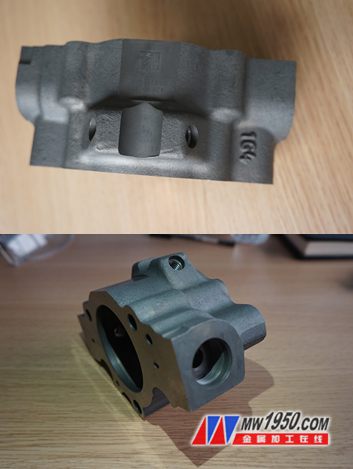
Figure 2. The material of the forged steel DCR product has high hardness, complex processing shape, and many deep holes and intersecting holes. The processing cost has always been high.
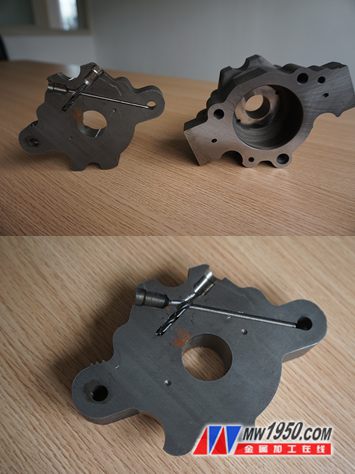
Figure 3. DCR pump cover, material hardness is 40HRC, with oblique cross holes, the angle is 120 degrees, the processing hole depth is 84mm, D4, 21 times diameter. Since the second hole is processed, because of the cross hole and the heat treatment hardness is relatively high, it is generally easy to break the knife, especially to check the centering of the drill bit and the support ability of the through hole edge belt. (The illustration shows the broken bit)
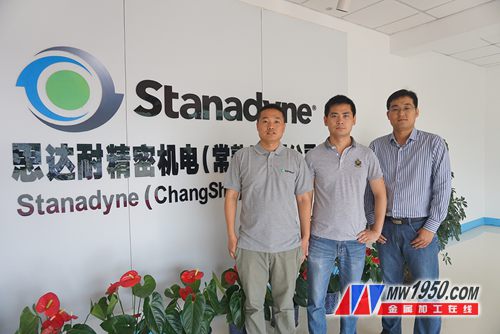
Figure 4: Ji Zengliang (middle), head of the Stanley supply chain optimization project, Tan Satisfaction (left) focuses on tool optimization. Xia Juntao (right) is Walter's senior technical expert in the Suzhou area.
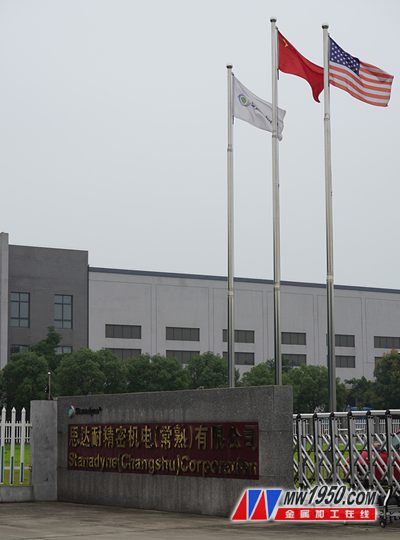
Figure 5: A project switches all the tools, usually at least half a year to a year, and Stanley has only completed in three months. This is a testimony to Changshu Sida's excellent management level and production level, and also a powerful explanation for its partner Walter's strength.
The main uses of carbide burrs:
Finish machining of various metal mold cavities; craft engraving of various metals and non-metals, engraving of craft gifts; cleaning up flash and welds of casting, forging, and welding parts, such as machine foundries, shipyards
Etc.; chamfering and rounding of various mechanical parts and processing of grooves, finishing of the inner hole surface of mechanical parts, etc.
Carbide Burr,Tungsten Carbide Cutting Tool,Double Machine Tool,Grinding Stone
Behappy Crafts (suzhou)Co.,Ltd , https://www.haoyuebehappy.com