A pump formed by two or three screws meshing together is called a screw pump.
A pump formed by two or three screws meshing together is called a screw pump. For a twin screw pump, the flow rate is: Q=3Ω/16(D2-d2)tn Where D is the outer diameter of the screw; D——the inner diameter of the screw; T——pitch; n - the number of revolutions. Ω≈3.14 This formula can be understood as: Ω/4 (D2-d2) is the area of ​​the ring between the inner and outer diameter of the screw. When the screw rotates one revolution, the end position does not change, but the liquid advances a pitch in the screw. Therefore, the volume of the liquid transported forward by the twin-screw one-time forward transfer is Ω/4 (D2-d2), and considering the volume occupied by the meshing portion is 1/4, so the volume of the transported liquid is 3/4. Ω/4(D2-d2)t. Multiply the number of revolutions n to the flow per minute. For the three-screw pump, the same understanding can be used to calculate, but the form of the screw must be clarified. Some of the outer diameters of the screw are equally large, and some (most) are smaller than the active rod. Actual traffic is different. Like the gear pump, the flow rate of the screw pump is a fixed value. Its characteristic curve is a vertical line. In order to prevent an excessive increase in the outlet pressure, the outlet should also be provided with a safety valve (which is constructed like a pressure relief valve). When the screw pump is working, the rotor is subjected to axial thrust. Therefore, some screw pumps have oil suction chambers at both ends of the screw, and the oil pressure chamber is located at the middle of the screw; the threads on both sides of each screw are reversed. Therefore, when rotating, the oil enters from both ends of the screw and flows out from the middle of the screw to balance the axial thrust. In order to eliminate the radial load acting on the active screw during the operation of the twin-screw pump, the pump can be designed in the form of a three-screw, with the active screw being placed between the two driven screws. The screw pump is characterized by good self-priming performance, no noise at work, long life and higher efficiency than the gear pump (0.70~0.95). It is used as an oil pump in a power plant, such as a main oil pump of a steam turbine and a main oil pump of some steam feed water pumps, that is, a screw pump. The gap measured by the screw pump during inspection is: 1. The radial clearance between the screw and the outer casing is generally 0.10~0.15 mm. Measure with a feeler gauge. 2. The top and side gaps at the meshing point between the screw and the screw are generally 0.10~0.15 mm. 3. The axial clearance between the driven screw shaft head and the outer casing is generally 2 ± 0.5 mm. 4. The bearing pad clearance is 0.08~0.12 mm. Hongling Pump & Valve Co., Ltd. Website: http:// |
Previous: Types of abnormal sounds that often occur in pump operation |
Next: |
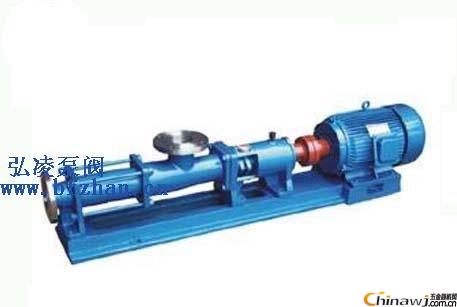
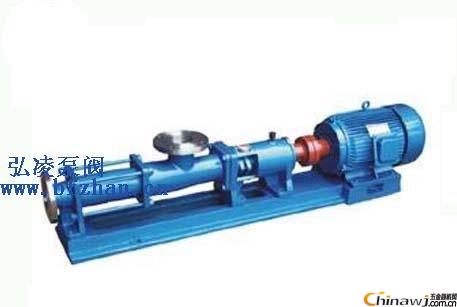
Hyundai Parts,Machinery Spare Parts,Hyundai Aftermarket Parts,Dump Truck Spare Parts
JINING SHANTE SONGZHENG CONSTRUCTION MACHINERY CO.LTD , https://www.sdkomatsuloaderparts.com